The working environment of glass kiln is very harsh, and the damage of kiln lining refractory material is mainly affected by the following factors.
(1) Chemical erosion
Glass liquid itself contains a large ratio of SiO2 components, so it is chemically acidic. When kiln lining material is in contact with the glass liquid, or under the action of the gas-liquid phase, or under the action of the scattered powder and dust, its chemical corrosion is severe. Especially at the bottom and side wall of the bath, where suffers molten glass liquid erosion in long term, the chemical erosion is more serious. The checker bricks of regenerator works under high temperature fume, gas and dust erosion, the chemical damage is also strong. Therefore, when selecting refractory materials, the resistance to corrosion is the most critical factor to be considered. The molten bath bottom refractory and side wall refractory should be acid. In recent years, fused cast AZS series bricks are the best choice for important parts of the molten bath, such as
zirconia mullite bricks and
zirconium corundum bricks, besides, high quality silicon bricks are also used.
Taking into account of the special structure of the glass kiln, the bath wall and bottom are made of large refractory bricks instead of small bricks, so the material is mainly fused cast.
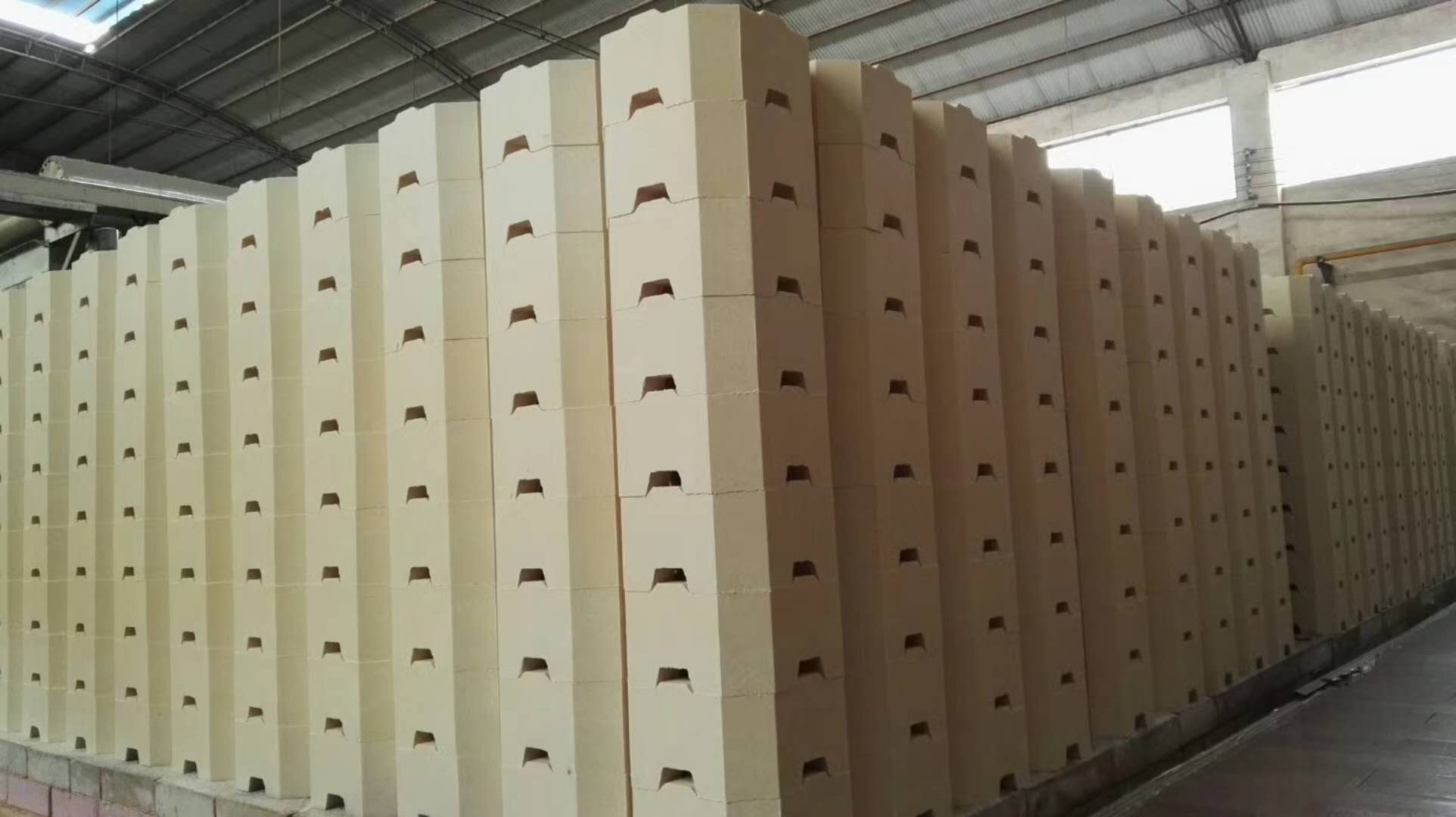
(2) Mechanical scouring
Mechanical scouring is mainly the strong scouring of molten glass flow, such as the kiln throat of the melting section. The second is the mechanical scouring of the material, such as the material charging port. So, refractories used here should have high mechanical strength and good scouring resistance.

(3) High temperature action
The working temperature of the glass kiln is as high as 1600 °C, and the temperature fluctuation of each part is between 100 and 200 °C. It should also be noted that the kiln lining works under long-term high-temperature conditions. Glass kiln refractory materials must be resistant to high temperature erosion, and should not contaminate glass liquid.